
Labeling Machine Benefits
In industries, a labeling machine stands as an automated marvel, precisely affixing labels or markings onto products or packaging. This versatile equipment caters to various label types—think self-adhesive, shrink-sleeve, and pressure-sensitive—while also offering customization options, ensuring labels adhere flawlessly to specific product areas like tops, bottoms, sides, or wraparound placements.
Industrial labeling machines find extensive application across sectors like food and beverage, cosmetics, pharmaceuticals, and consumer goods. Their primary role? Elevating operational efficiency and precision by streamlining labeling processes, curtailing manual intervention, and ramping up production velocity. These machines often boast advanced functionalities encompassing barcode scanning, printing capabilities, data printing, and visionary systems, ensuring impeccable label positioning and slashing error margins.
Beyond their core function of label application, these industrial labeling machines perform a diverse range of tasks. From coding and marking to enabling traceability and facilitating seamless product identification, they serve as multifaceted assets in industrial operations.
Table of Contents
What is a labeling machine?
A labeling machine is a device used to apply labels onto various items, products, or packaging. It automates the process of attaching labels, ensuring accuracy and efficiency in industries such as manufacturing, packaging, and distribution. These machines can handle different types of labels—adhesive stickers, tags, sleeves, or wraps—and can be customized to apply them to different surfaces, shapes, and sizes of products. They vary in complexity, from manual or semi-automatic machines suitable for small-scale operations to fully automated systems for high-volume production lines.
Why is labeling machine important?
Labeling machines play a crucial role in industries for several reasons:
- Efficiency: These machines streamline the labeling process, significantly reducing the time and effort required for manual application. They ensure swift and consistent label placement, especially in high-volume production environments.
- Accuracy and Consistency: Labeling machines are designed to apply labels with precision and uniformity. This consistency is crucial for compliance with regulations, maintaining product quality, and reinforcing brand identity.
- Compliance and Traceability: They help companies adhere to industry standards and regulations by ensuring accurate labeling of crucial information such as ingredients, nutritional facts, expiration dates, and barcodes. This aids in traceability and product safety.
- Enhanced Branding: Well-designed, eye-catching labels created by these machines contribute to improved product visibility and branding. They make products more appealing to consumers, potentially boosting sales.
- Operational Streamlining: By automating the labeling process, these machines free up human resources for more complex tasks, contributing to overall operational efficiency and cost-effectiveness.
- Adaptability: Labeling machines can handle various label types and materials, accommodating different packaging formats and product specifications.
Overall, these machines are instrumental in improving productivity, ensuring compliance, enhancing product presentation, and contributing to the overall success of businesses in numerous industries.
Type of Labeling machine
Labeling machines come in diverse types, tailored for specific labeling needs:
- Roll-fed Labeling Machine: Utilizing a roll of self-adhesive labels, this machine swiftly applies them to products in motion along a conveyor. Ideal for high-speed labeling tasks.
- Pressure-sensitive Labeling Machine: Applying self-adhesive labels using pressure, this type caters to both flat and round products, commonly favored in cosmetic and personal care sectors.
- Shrink-sleeve Labeling Machine: These machines affix heat-shrinkable labels to products, ensuring a snug fit through heat application—a popular choice for various products.
- In-mold Labeling Machine (IML): Employing the in-mold labeling process, this machine embeds labels into the mold of plastic products during manufacturing. The resulting label becomes an integral part of the product, ensuring durability and a polished appearance.
- Wraparound Labeling Machine: Tailored for round containers and bottles, these machines apply labels by encircling the product, ensuring comprehensive coverage.
- Automatic Labeling Machine: Fully automated, these machines handle diverse labeling functions—placement, printing, inspection—ideal for high-volume production setups where precision and swiftness are paramount.
Each machine type boasts distinct features and capabilities, chosen based on product type, size, label specifications, and production speed and volume. The selection hinges on aligning the machine’s capabilities with the specific requirements of the labeling task at hand.
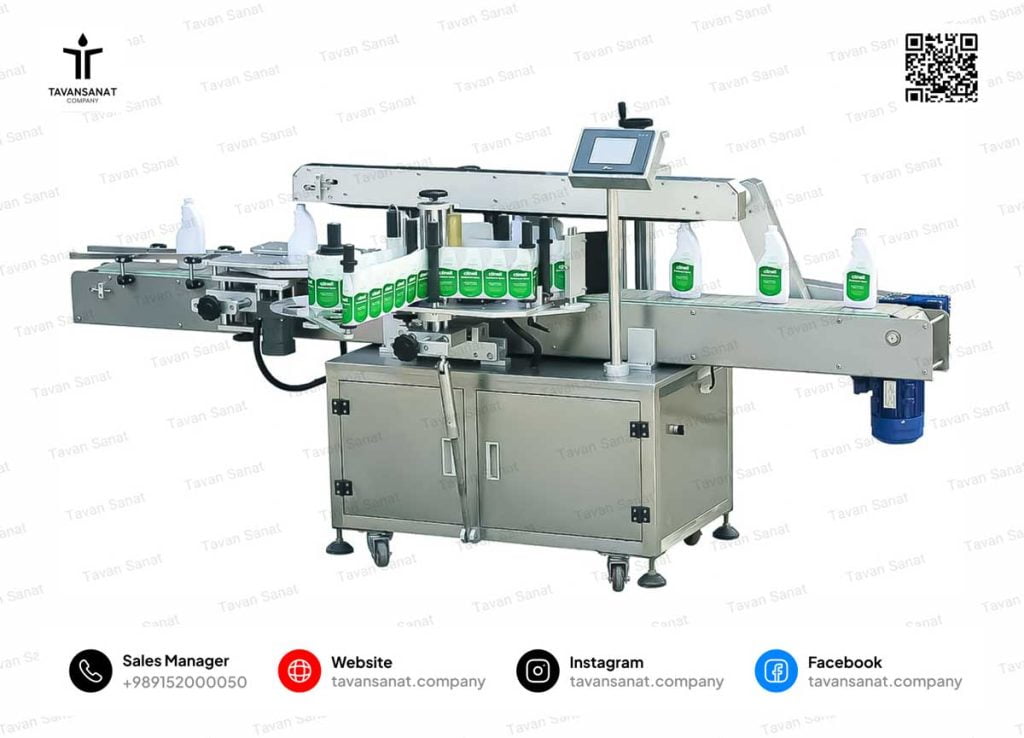
Labeling machines in Food and beverage industry
Within the food and beverage industry, labeling systems are pivotal, given the stringent and intricate labeling regulations. Here are common machine types employed:
- Roll-fed: Widely used for applying self-adhesive labels to food and beverage packaging like boxes, cans, bottles, and jars. Recognized for speed and efficiency, perfect for high-volume applications.
- Shrink-sleeve: Tailored for affixing heat-shrinkable labels to containers. Ideal for round containers, ensuring a snug fit and presenting a high-quality, tamper-evident facade.
- Wraparound: Commonly employed for round containers such as bottles, cans, and jars, applying labels by encircling the container. Offers a high-quality appearance and ample space for displaying information.
- Automatic: Fully automated, these machines handle multifaceted tasks—label placement, printing, inspection—catering to diverse needs like barcode, expiration date, and nutrition information printing in high-volume production environments.
Adherence to rigorous food safety standards is imperative in these machines. They must be easy to clean and sanitize while enduring harsh production settings and exposure to heat, moisture, and contaminants. Precision in label application and ensuring clear, legible printing, especially for critical information like ingredients, allergens, and nutrition details, is paramount.
automatic and semi-automatic labeling machines
Efficient and precise, automatic and semi-automatic labeling systems vary in their level of automation:
Automatic Labeling Machines: These are fully automated systems adept at managing various labeling functions—placement, printing, inspection—ideal for high-volume production setups. While pricier, they offer heightened efficiency and accuracy, catering to diverse labeling needs like barcode, expiration date, and nutrition info printing.
Semi-Automatic Labeling Machines: Requiring some manual intervention, these machines might necessitate manual loading, product alignment, or label adjustments. Although slower than automatic counterparts, they present a more budget-friendly option, especially suitable for lower production volumes or customization-heavy labeling tasks.
Both systems can be tailored to meet industry-specific needs, whether it involves applying shrink-sleeve, wrap-around, or roll-fed labels. They ensure efficient and accurate labeling, contributing to enhanced company productivity. Choosing between automatic and semi-automatic labeling machines hinges on production volume, labeling requisites, and the company’s budget considerations.
Advantages of Labeling machines in the industry
There are several advantages to using a this machine in the industry, including:
Increased Efficiency: Labeling machines can increase the speed and efficiency of the labeling process, reducing the need for manual labor and increasing production speed.
Improved Accuracy: Labeling machines are designed to ensure accurate label placement and reduce the risk of errors, improving the quality and consistency of the labeling process.
Increased Productivity: By automating the labeling process, labeling machines can increase overall productivity, freeing employees to focus on other tasks.
Reduced Costs: By reducing the need for manual labor and increasing production speed, labeling machines can help reduce costs associated with the labeling process.
Enhanced Traceability: Labeling machines can be equipped with barcode scanning and printing capabilities, making it easier to track products and maintain accurate records for traceability purposes.
Better Branding: Labeling machines can apply high-quality, eye-catching labels to products, enhancing the overall appearance and promoting the brand.
Compliance with Regulations: Labeling machines can be designed to meet strict labeling regulations and requirements, helping companies comply with industry standards and regulations.
Improved Product Safety: By accurately applying labels with important information, such as ingredient lists, allergens, and nutrition information, labeling machines can enhance product safety and reduce the risk of errors.
Overall, employing this technology in the industry can provide numerous benefits, including increased efficiency, improved accuracy, and enhanced traceability, aiding companies in streamlining their operations and enhancing their bottom line.
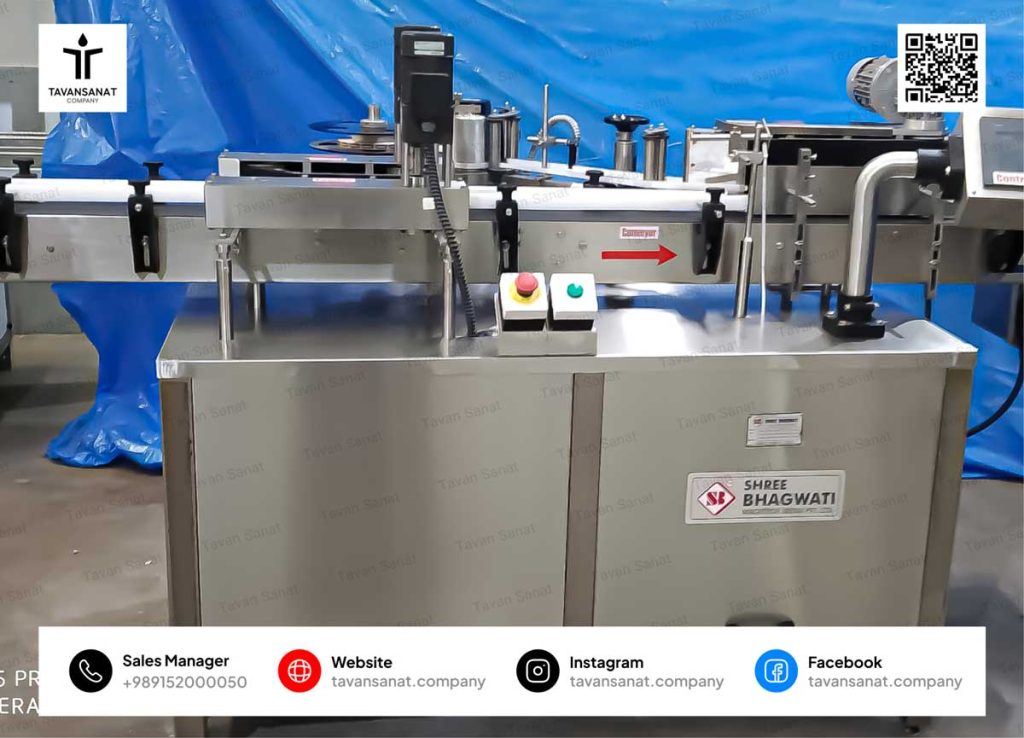
Conclusion of this article
In a multitude of industries, particularly the food and beverage sector, the significance of specialized systems that streamline the labeling process cannot be overstated. These purpose-built mechanisms serve as the linchpin for expediting labeling procedures while concurrently elevating the overall efficiency, precision, and consistency of the labeling process.
The fundamental objective of these sophisticated apparatuses extends beyond mere expediency. They also serve as guardians of traceability and product safety, pivotal facets in industries governed by stringent regulatory frameworks. For comprehensive insights into integrating these systems seamlessly into operational paradigms, seeking guidance and support from Tavansanat Company of experts stands as an invaluable resource.
Moreover, these labeling systems function as agents of compliance, facilitating adherence to industry regulations, standards, and protocols. Concurrently, they contribute significantly to augmenting brand identity and market presence through the application of high-quality, visually compelling labels.
The adaptability of these systems proves indispensable, catering seamlessly to diverse label types—be it the application of shrink-sleeve, wrap-around, or roll-fed labels—delivering multifaceted advantages that transcend mere expediency.
At their core, these specialized tools represent more than just operational aids. They embody strategic assets that underpin the optimization of company operations, enhancing overall efficiency, and invariably bolstering the bottom line. Their pervasive influence across the operational spectrum makes them an integral and indispensable facet for enterprises seeking operational fluidity and sustainable growth in competitive market landscapes.